轴悬式驱动方式


轴悬式驱动方式,又名为抱轴式、吊挂式、电车式、鼻悬式、半悬挂式驱动方式,是铁路机车车辆上应用历史最悠久的牵引传动装置类型之一,该驱动方式的特点是将牵引电动机的一侧通过轴承刚性地抱合在车轴上,而牵引电动机的另一端则弹性悬挂于转向架构架,牵引电动机大多采用平行于车轴的布置方式。轴悬式驱动装置最早在十九世纪末首先应用于城市有轨电车,由于其结构简单和成本低廉等优点,迅速普及应用到各类型的电传动铁路机车和动车,过百年来一直沿用至今。
刚性轴悬式
[编辑]结构特点
[编辑]
A:牵引电动机
B:牵引电动机弹性悬挂装置(吊鼻)
C:车轴
D:大齿轮
E:小齿轮
G:转向架构架

刚性轴悬式传动装置是在1885年由美国发明家法蘭克·史伯格发明(美国专利号:US 324892 A[1]),并在两年后首次在美国維珍尼亞州的里士满联合客运铁路得到应用,这也是世界上第一个投入营运的有轨电车系统[2]。此后,轴悬式传动装置随着有轨电车的浪潮而推广到世界各地,并且在铁路机车和电力动车组上被广泛使用。
牵引传动装置的作用是将牵引电动机所产生的旋转力矩传递给轮对,而轴悬式驱动装置的主要结构如前所述,牵引电动机的一侧通过轴承刚性地抱合在车轴上,而牵引电动机的另一端则通过悬挂装置弹性地悬挂于转向架构架的横樑或端樑。这类型传动装置一般采用单级减速齿轮传动,整套装置由主动齿轮(小齿轮)、从动齿轮(大齿轮)、齿轮箱体、抱轴箱体等部分组成,小齿轮装配在牵引电动机电枢轴上以传递旋转扭矩,再将扭矩传递给固定压装在车轴上的大齿轮[3]。牵引电动机可以通过弹性悬挂装置作纵向和横向摆动,弹性悬挂装置的结构形式林林总总,例如螺旋弹簧式、弹簧套筒式、橡胶缓冲器等。牵引电动机通常采用平行于车轴的布置方式,但也有例子将牵引电动机布置在车辆纵向中心线方向,并通过锥齿轮或蜗轮传动车轮,这种纵向形式的布置在有轨电车的应用较多,原因是车轮直径可以不受牵引电动机直径的限制,允许使用小直径车轮以降低登车高度,典型例子有苏黎世交通局Be 4/4型有轨电车。[4]。
轴悬式驱动装置的主要优点是结构简单、安装容易、维修方便。此外,轴悬式驱动装置还具有结构紧凑、便于充分利用空间的优势,由于齿轮中心距(车轴和电机轴之间的距离)较短,只需采用单级减速齿轮传动,就保证能够在最小的空间内安装牵引电动机,并且可以设计较大的齿轮传动比和较小的车轮直径。然而,由于牵引电动机的约一半重量属于簧下重量,导致轴悬式驱动装置产生很大的轮轨作用力,而且轮轨作用力随着车辆速度的提高而增大,过大的轮轨作用力会对线路上部建筑造成破坏,导致线路品质恶化和加剧车辆损耗。同时,车轮与钢轨之间的动力作用直接传到牵引电动机,使牵引电动机和传动齿轮直接承受来自轮对的振动,导致牵引电动机振动加速度以及传动齿轮啮合面接触动应力增大,影响牵引电动机和驱动装置的工作可靠性及使用寿命。除此之外,由于齿轮啮合时齿与齿之间的振动冲击,轴悬式驱动装置运转时也会产生较大的齿轮噪音[4]。
簧下重量过重是限制了刚性轴悬式驱动装置使用范围的一个重要原因,它并不适合用于最高速度达140公里/小时以上的快速铁路车辆;而对于结构速度较低的铁路车辆(最高速度不大于120公里/小时),轴悬式驱动仍然不失为一个简单可靠的选择[3]。当机车车辆进入交流传动的时代以后,重量较轻的交流牵引电动机能够减少簧下重量,有助降低轴悬式驱动装置对轨道的动力作用,例如采用轴悬式驱动的西门子ES64F、ES64F4型电力机车,其最高速度可达到140公里/小时,这基本上已经是轴悬式驱动装置的极限。为了解决轴悬式驱动装置簧下重量大的缺点,其中一个解决方法是将牵引电动机整体悬挂在转向架上,并与属于簧下重量的车轴采用弹性联接,即架悬式驱动方式。
抱轴轴承
[编辑]轴悬式驱动装置根据所使用的抱轴轴承类型,可分为采用滑动轴承的滑动抱轴,或者采用滚动轴承的滚动抱轴两种形式。在二十世纪中期之前各国大多采用成本较低的滑动轴承,但滑动轴承的主要缺点是需要较多的维护保养,这是因为轴承和车轴之间间隙的大小,会随着运行公里数和抱轴瓦磨耗的增加而增大,导致齿轮副中心距改变和齿轮啮合条件恶化,因此必须经常对滑动轴承进行检查维护,确保齿轮达到应有的使用寿命[3]。为了克服这一缺点,二十世纪中期以后开发的轴悬式驱动装置,许多都改为使用少维护或免维护的滚动轴承。在此之前主要有两个原因阻碍滚动抱轴的应用,其一是滚动轴承外径相对滑动轴承较大,而传动装置齿轮副轴距一般都比较小,其二是铁路车辆使用的滚动轴承必须具备良好的密封性能,防止运转时外部灰尘、异物、水分等侵入轴承内部。这些问题随着二战以后轴承技术的快速发展,例如采用双列球面滚子轴承、迷宫式轴承密封装置而得到解决[3]。
传动方式
[编辑]
轴悬式驱动装置可以依机车车辆的技术要求或转向架结构,设计成单侧齿轮单边传动或双侧齿轮双边传动。双边传动的两组传动齿轮分别安装在牵引电动机的两侧,这种结构的优点是轮对的左右扭矩均衡,并可以传递较大的旋转力矩,但缺点是占用较多轮对内侧有限的轴向空间,因而对牵引电动机的尺寸有更严格的限制,不利于进一步提高单轴功率。双边传动一般均使用斜齿圆柱齿轮,而且双侧齿轮的齿斜相反,因此双侧齿轮的轴向力也相反,齿轮安装的误差可由轴向力差值引起的轮对微小横动来得到纠正,保证了双侧齿轮传动转矩的均匀性。如果采用双侧直齿轮,轮对组装时必须保证双侧大小齿轮形对应的精确性,否则必然引致齿轮不能同时啮合,或双侧齿轮啮合力不等的问题。双侧斜齿传动的典型车型主要包括苏联铁路的K型、VL8型、VL22型、VL60型、VL80型电力机车,以及中国铁路的韶山1型、韶山3型电力机车。苏联曾经在部分VL8型、VL22M型电力机车试用双侧弹性直齿传动,但因结构复杂及装配困难等原因而被放弃[3]。
在采用轴悬式驱动装置的铁路机车车辆之中,采用双边齿轮传动的车型仅属少数,主流仍然是结构较为简单的单边齿轮传动,而且几乎无一例外地采用直齿圆柱齿轮。由于单边传动比双边传动少了一对齿轮,因此可以装用尺寸和功率较大的牵引电动机,而且簧下重量也相对地略为减轻,制造和装配工作亦较为简单。而缺点是传动时轮对受到偏于一侧的驱动力,抱轴承会承受不均匀的载荷,为此,可采用鼓形齿或斜边齿等齿向修正,或者采用滚动抱轴承等对策措施,确保齿轮对的正确啮合[3]。
弹性齿轮
[编辑]为了避免使传动齿轮直接承受来自轨道的振动冲击、延长齿轮和牵引电动机的使用寿命,自1920年代起,越来越多机车车辆的轴悬式驱动装置采用了弹性齿轮,以取代无弹性减震装置的刚性齿轮。这是提高机车走行部可靠性和耐久性的重要措施之一,弹性齿轮能够改善牵引齿轮间的偏载、缓和来自线路的动力冲击、改善牵引电动机的工作条件、减少由于齿轮制造和装配误差所引起的动力负荷等[5]。制造商一般都会选择将大齿轮设计成弹性结构,因为它有较大的空间设置弹性元件。弹性元件设置在齿轮圈和齿轮心之间,较常见的弹性元件包括金属片弹簧、金属圆弹簧和橡胶弹簧。
金属片弹簧弹性齿轮由瑞士机车和机器制造厂(SLM)发明,最初使用于瑞士BLS铁路的Be 5/7型电力机车;这种弹性齿轮实际上衍生自阿普特式齿轨铁路机车的牵引齿轮,使用多层弯曲的钢板弹簧作为弹性元件,但由于钢板弹簧刚度大、缓冲效果不显著、组装及维修不方便,因此这种弹性齿轮在二十世纪中叶以后已被逐步淘汰,典型例子有瑞士为罗马尼亚研制的060 DA型柴油机车[6]。
金属圆弹簧弹性齿轮于1920年代由美国西屋电气公司发明,最早使用于鲍尔温机车厂及西屋电气公司制造的日本國鐵EF51型電力機車,这种弹性齿轮采用螺旋圆弹簧作为弹性元件,并且可以配合额外的摩擦式阻尼装置,来获得合适的性能参数。在1930年代至1950年代,金属圆弹簧弹性齿轮的制造技术已发展成熟,法国、日本、苏联、英国等国亦广泛采用了这种结构[3]。
套筒形橡胶元件弹性齿轮于1930年代在英国面世,最初被使用于英国城市有轨电车上。由于橡胶元件弹性齿轮结构简化、制造成本降低,而且橡胶元件也不像金属弹簧那样需要经常维护,因此自1950年代起开始迅速普及,并出现逐步取代金属弹簧弹性齿轮的趋势。例如,日本首先在日本國鐵EF58型電力機車上,进行了套筒形橡胶元件弹性齿轮的运用试验,并自1960年代起应用到EF70型及以后的各型电力机车。而苏联则从1974年开始,在所有新造的2TE10V、2TE116型货运机车,以及TEM7型调车机车上应用自动调节式橡胶元件弹性齿轮。
弹性轴悬式
[编辑]结构特点
[编辑]弹性轴悬式驱动方式又称为弹性半悬挂传动,是从上述的刚性轴悬式驱动装置的基础上发展而成。这种驱动装置的特点是,牵引电动机与转向架之间的鼻式悬挂方式原则上保持不变,但牵引电动机抱轴承不再直接由车轴支撑,而是支撑在一根同心地包在车轴外的空心轴上,从动大齿轮固定安装在空心轴端部,空心轴两端通过弹性元件支承在车轮心上,牵引电动机输出的力矩通过小齿轮传至大齿轮,通过空心轴、弹性元件传至轮对,空心轴与车轴一同旋转[7]。虽然牵引电动机约一半重量仍然支承在车轴上,但之间通过具有缓冲作用的弹性元件,使抱轴载荷能够弹性地支承于车轴上,故称之为弹性轴悬式。因此,弹性轴悬式的重点在于联接空心轴和轮心的弹性元件,它既要支承牵引电动机约一半的重量和空心轴及大齿轮的全部重量,并且具有可适应各个方向运动和衰减振动的功能,还要传递牵引电动机通过大齿轮传来的力矩。空心轴与车轴之间的间隙一般为15毫米左右,约为轮对空心轴架承式驱动方式的三分之一[8]。
弹性轴悬式传动装置除继承了刚性轴悬式结构简单的优点,并且令牵引电动机的全部重量都属于簧上重量,来自钢轨的硬性冲击经过弹性元件的缓冲,有效缓和了轨道不平顺对牵引电动机的振动冲击,使牵引电动机和传动齿轮的运转条件得以改善。此外,这类型采用橡胶弹性元件的弹性传动装置还具有很大的扭转弹性,当车辆进行起动时动轮尚未转动之前,牵引电动机整流子已经开始相对转动,以德国联邦铁路E40型电力机车为例,当起动牵引力达到75千牛时,电枢已经首先转动过了27个整流子片,使每一整流子片仅在极短时间内承受较大的起动电流,从而对牵引电动机产生了保护作用;而且橡胶弹性元件的旋转弹性也有利于起动,即使稍微超过粘着系数时也不会发生轮对空转;基于同一原因,由牵引电动机产生双倍于电网频率的脉动转矩,其所引起振动亦得以通过弹性元件阻尼被衰减。
刚性轴悬式驱动装置对牵引电动机最大振动加速度,几乎是与轨道干扰作用同时发生;而弹性轴悬式驱动装置因弹性元件的阻隔作用,使牵引电动机达到最大振动加速度的时间得以延迟,牵引电动机相对动轴的位移在其固有振动的四分之一周期以后才达到最大值。然而,弹性轴悬式本质上仍然属于轴悬式驱动,弹性元件的挠度远比一系悬挂为小,因此对牵引电动机的振动冲击不可能完全消除,减震效果与全悬挂驱动装置相比仍有差距[7]。另一方面,由于空心轴与车轴之间的间隙较小,因此牵引齿轮副中心距也相对较小,难以设计尺寸较大的小齿轮和较小的传动比,不利于进一步提高机车车辆的构造速度,使其应用范围受到一定限制。
弹性轴悬式的典型例子有瑞典通用电机公司(ASEA)的橡胶盘式弹性驱动装置、瑞士欧瑞康机械制造厂(MFO)的柱销式弹性联轴装置、西德西门子-舒克特公司(SSW)的环状橡胶弹性驱动装置、东德黑尼格斯多夫电力机车制造厂(LEW)的锥形橡胶环弹性驱动装置,大多用于构造速度为120~160公里/小时的铁路机车车辆。弹性轴悬式驱动的概念始于1930年代,至1948年首次应用于瑞典国铁的X5型电力动车组[9]。1950年代,西门子-舒克特公司发明了环状橡胶弹性轴悬式驱动装置,并且被广泛运用于德国联邦铁路的标准化电力机车系列。1960年代,黑尼格斯多夫电力机车厂参照西门子的产品,研制了锥形橡胶环弹性轴悬式驱动装置;随后,日本亦成功研制了QD10型弹性轴悬式传动装置,被装用于日本國鐵EF66型電力機車[10]。
SSW传动装置
[编辑]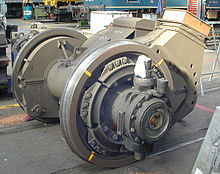
1950年,联邦德国(西德)的西门子-舒克特公司(SSW)成功研制了环状橡胶弹性驱动装置(德語:Gummiringfederantrieb),又称为西门子-舒克特传动装置或简称SSW传动装置。这种弹性轴悬式驱动装置的特点是采用了西门子独创的扇形橡胶块作为弹性元件,传动系统由齿轮副、空心轴和每侧六组扇形橡胶块组成。牵引电动机的一端通过剪切橡胶弹簧悬挂于转向架构架,另一端通过滚动轴承和空心轴套座落在圆柱形空心轴,空心轴套用螺栓与牵引电动机机座相连,而大齿轮的齿轮心用12个螺栓固定在空心轴两端;从齿轮心伸出来六个臂爪,通过六组呈环状布置的扇形橡胶块,与车轮心的辐板联接及传递扭矩。
西门子-舒克特传动装置首先被安装在德国联邦铁路E44 038号机车的其中一台转向架上,进行了弹性轴悬式和刚性轴悬式的对比试验。试验结果显示,弹性轴悬式驱动装置对于牵引电动机有明显的减震作用,垂直振动加速度是刚性轴悬式的五分之一,水平振动加速度是刚性轴悬式的六分之一[8]。与此同时,在德国联邦铁路E10.0型电力机车的首五台原型车上,其中一台机车亦采用了西门子舒克特传动装置,与其他机车使用的三种传动装置进行了对比试验[11] 。德国联邦铁路根据其试验结果,决定在自1956年起投入批量生产的标准化电力机车上,包括E10、E40、E41、E50型电力机车等,以及后来的111、151型电力机车,均统一采用西门子-舒克特传动装置。
LEW传动装置
[编辑]1960年,东德的黑尼格斯多夫电力机车制造厂(LEW)研制了锥形橡胶环弹性驱动装置(德語:Kegelringfeder-Antrieb),又简称为LEW传动装置,其技术结构与西门子-舒克特传动装置相类似,但改为使用一个具有30°锥角的整圈锥形橡胶环作为弹性元件。在运行速度为100公里/小时的动力作用条件下,锥形橡胶环的垂向挠度可达10毫米,轴向挠度可达8毫米。与SSW传动装置的扇形橡胶块相比,锥形橡胶环的结构和组装更为简单,但因橡胶环直径达600~700毫米,制造品质均匀的橡胶环的难度和成本亦较大。锥形橡胶环弹性驱动装置首先应用于1961年试制的德国国营铁路E11 002号电力机车原型车[12],并与装用刚性轴悬式驱动装置的E11 001号机车进行了对比试验。后来,锥形橡胶环弹性驱动装置被广泛使用于批量生产的德国国营铁路243、250、252型电力机车。
参考文献
[编辑]- ^ sprague US 324892 A. Google. [2015-08-04]. (原始内容存档于2016-07-02).
- ^ Ursula Grablechner. 120 Years of Electric Subways (PDF). hi!tech (Siemens). 2010年3月: 48.[永久失效連結]
- ^ 3.0 3.1 3.2 3.3 3.4 3.5 3.6 柳宇刚、顾振国. 《牵引传动装置》. 北京: 中国铁道出版社. 1985: 9-17 (中文(简体)).
- ^ 4.0 4.1 卡尔·萨克斯. 孙翔 , 编. 《电传动机车转向架结构与原理(下册)》. 北京: 中国铁道出版社. 1988: 18-38 (中文(简体)).
- ^ 黎冠中、戚文星. 日本防振橡胶弹性牵引齿轮的研制. 《国外内燃机车》 (大连: 铁道部大连内燃机车研究所). 1981年11月. ISSN 1003-1839.
- ^ Karl Sachs. Elektrische Triebfahrzeuge. Ein Handbuch für die Praxis sowie für Studierende. Berlin, Germany: Springer-Verlag. 1973. ISBN 9783211810729 (德语).
- ^ 7.0 7.1 Andreas Steimel. Electric Traction - Motive Power and Energy Supply: Basics and Practical Experience. München, Germany: Oldenbourg Industrieverlag. 2008: 37-41. ISBN 9783835631328 (英语).
- ^ 8.0 8.1 卡尔·萨克斯. 孙翔 , 编. 《电传动机车转向架结构与原理(下册)》. 北京: 中国铁道出版社. 1988: 38-46 (中文(简体)).
- ^ 柳宇刚、顾振国. 《牵引传动装置》. 北京: 中国铁道出版社. 1985: 17-20 (中文(简体)).
- ^ 井上等. 貨物の高速輸送と 2人力のマンモス・ロコEF90形機関車. 《交通技術》 (交通協力會). 1966年6月: 22–25 (日语).
- ^ Ralf Rossberg. Deutsche Eisenbahnfahrzeuge von 1838 Bis Heute. Berlin, Germany: Springer-Verlag. 2013: 183-185. ISBN 9783642957703 (德语).
- ^ Bedienungsanleitung (PDF). Tillig. [2015-08-04]. (原始内容存档 (PDF)于2019-06-30).